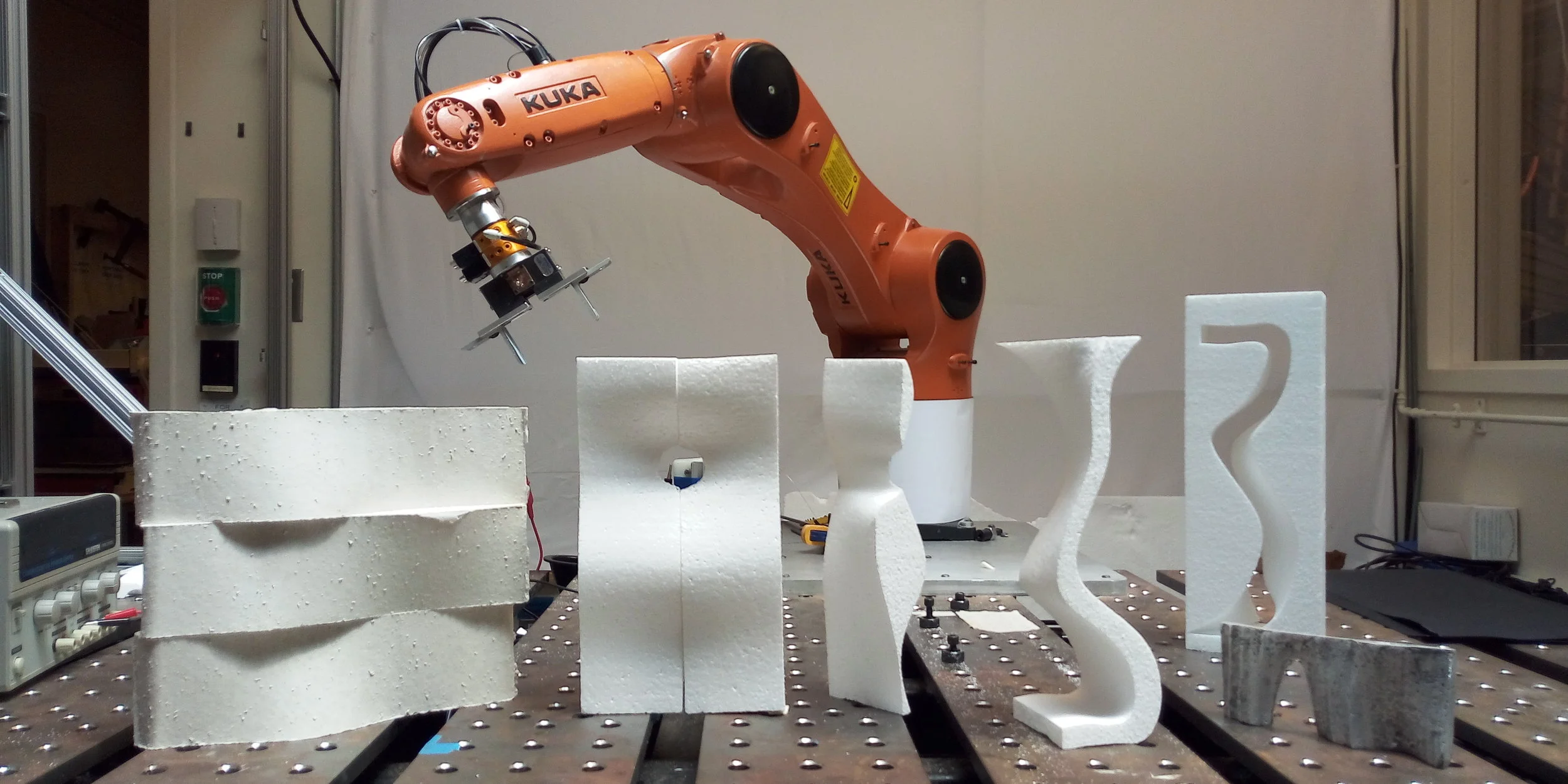
Robotic Foam Cutting
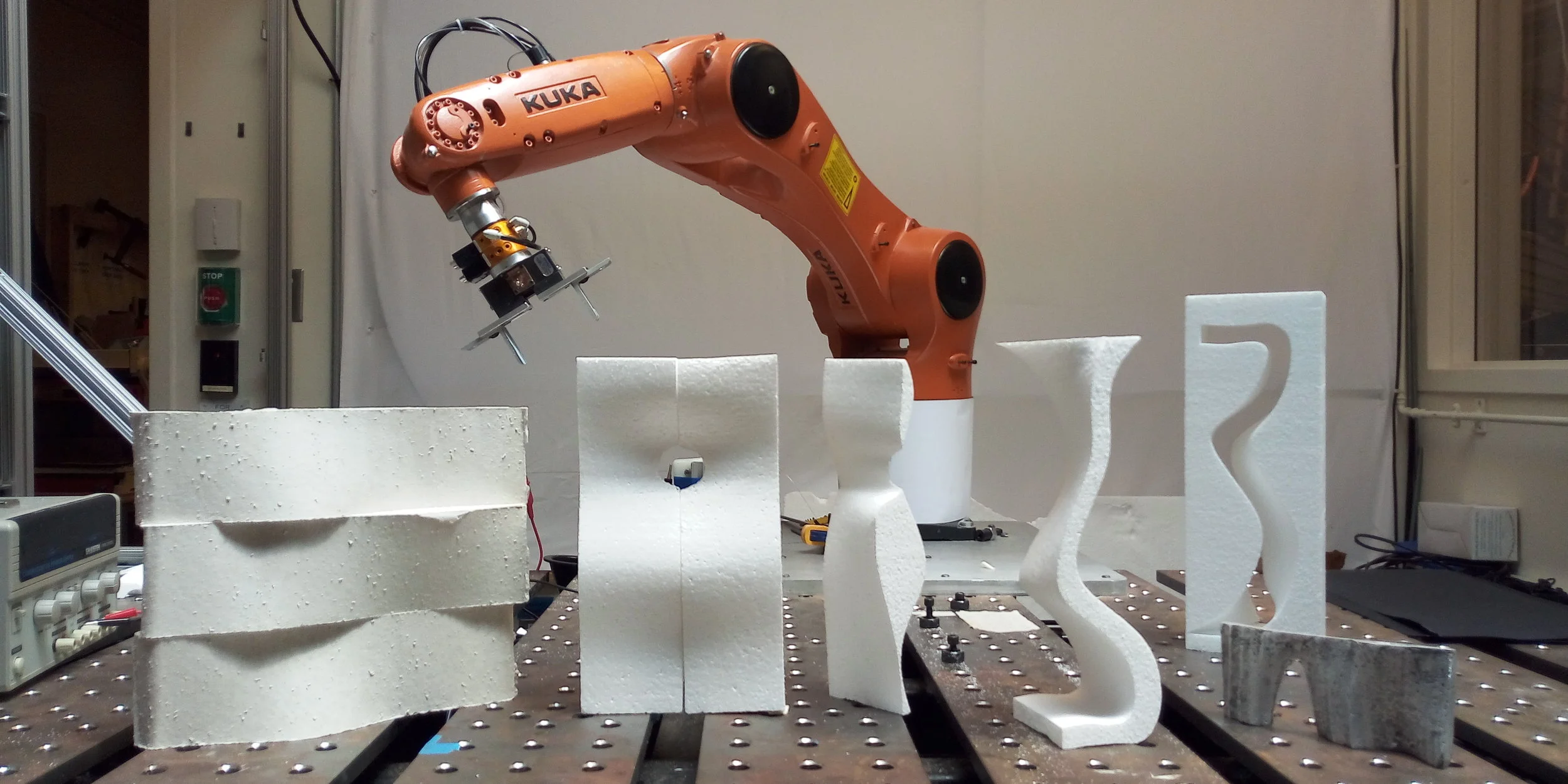
For our Design for Robotic Assembly course, we wanted to program our 6-axis robot to cut styrofoam blocks with a heated wire. Our hope was to cut geometries in a more accurate and faster method than a CNC mill.
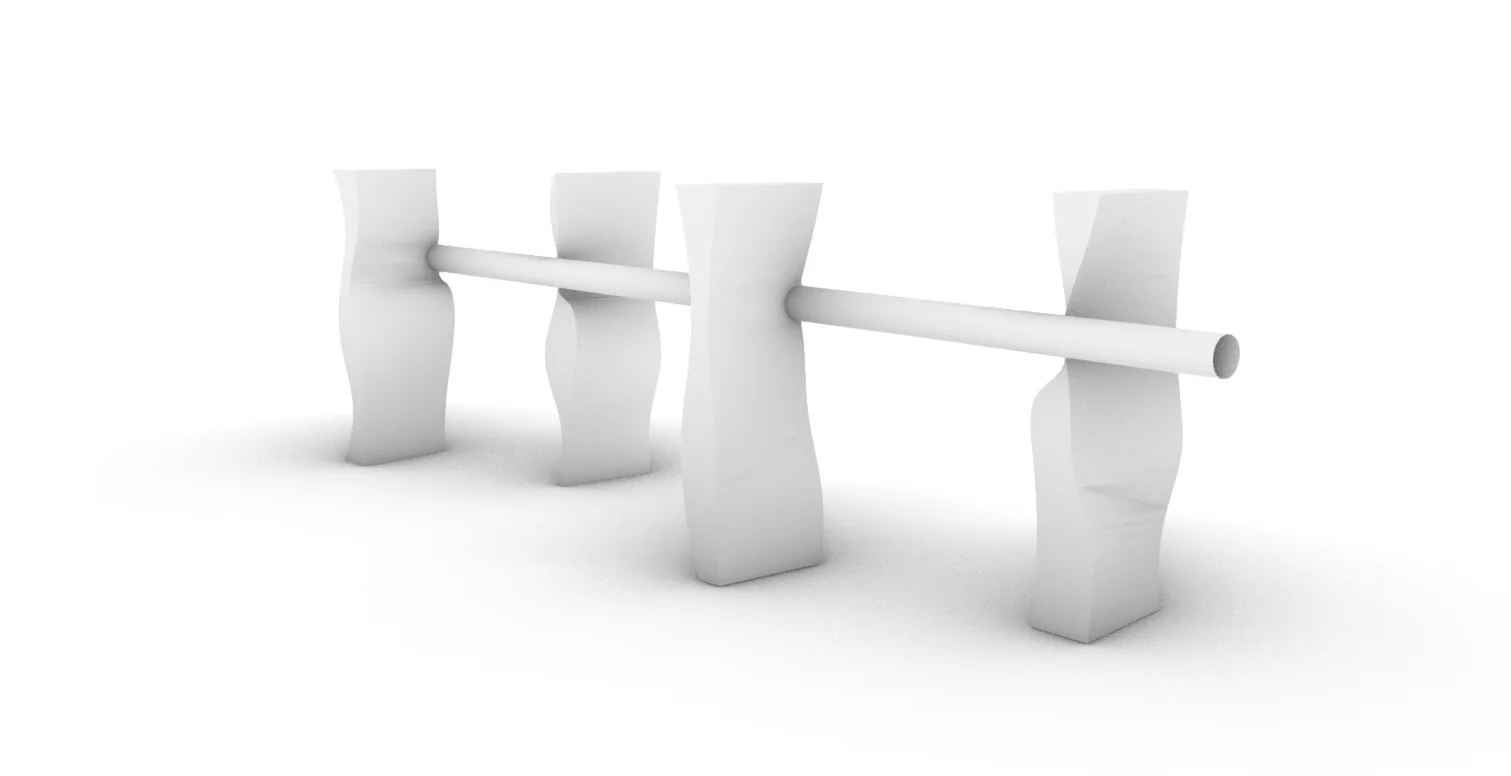
Our intention was to fabricate a series of ruled surface geometries that could be used in a furniture-like application

We generated a series of geometries using two curved surfaces, whose intersections generated a perfect semi-circular vacancy. We also checked the curvature of the planes to make a smooth, natural shape.
![180521_o2 [Converted].jpg](https://images.squarespace-cdn.com/content/v1/5a64f5f08a02c74bc460d658/1527390836316-LFFW4ACB505X9GUI79H6/180521_o2+%5BConverted%5D.jpg)
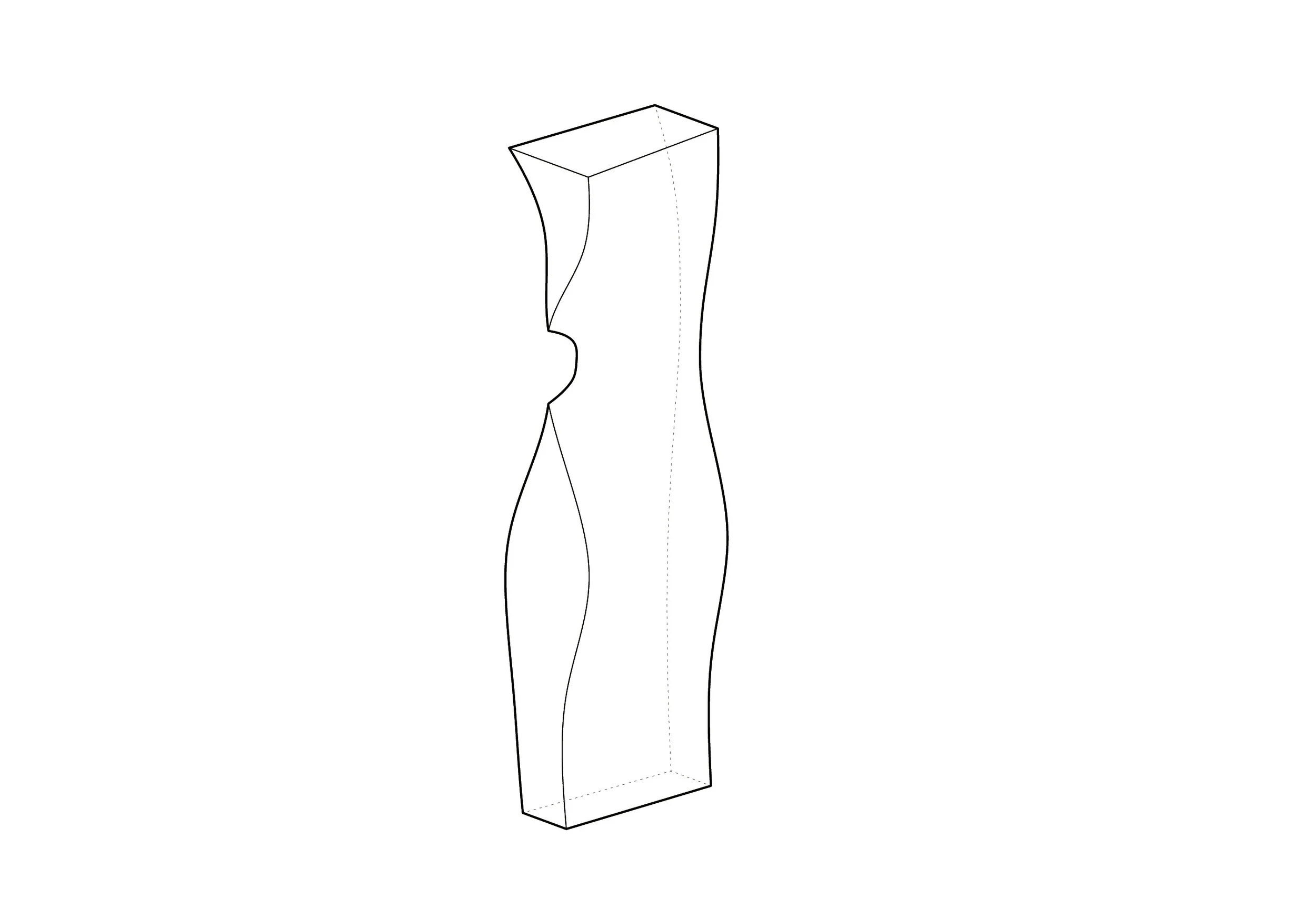
An example of a final geometry cut with our robot.
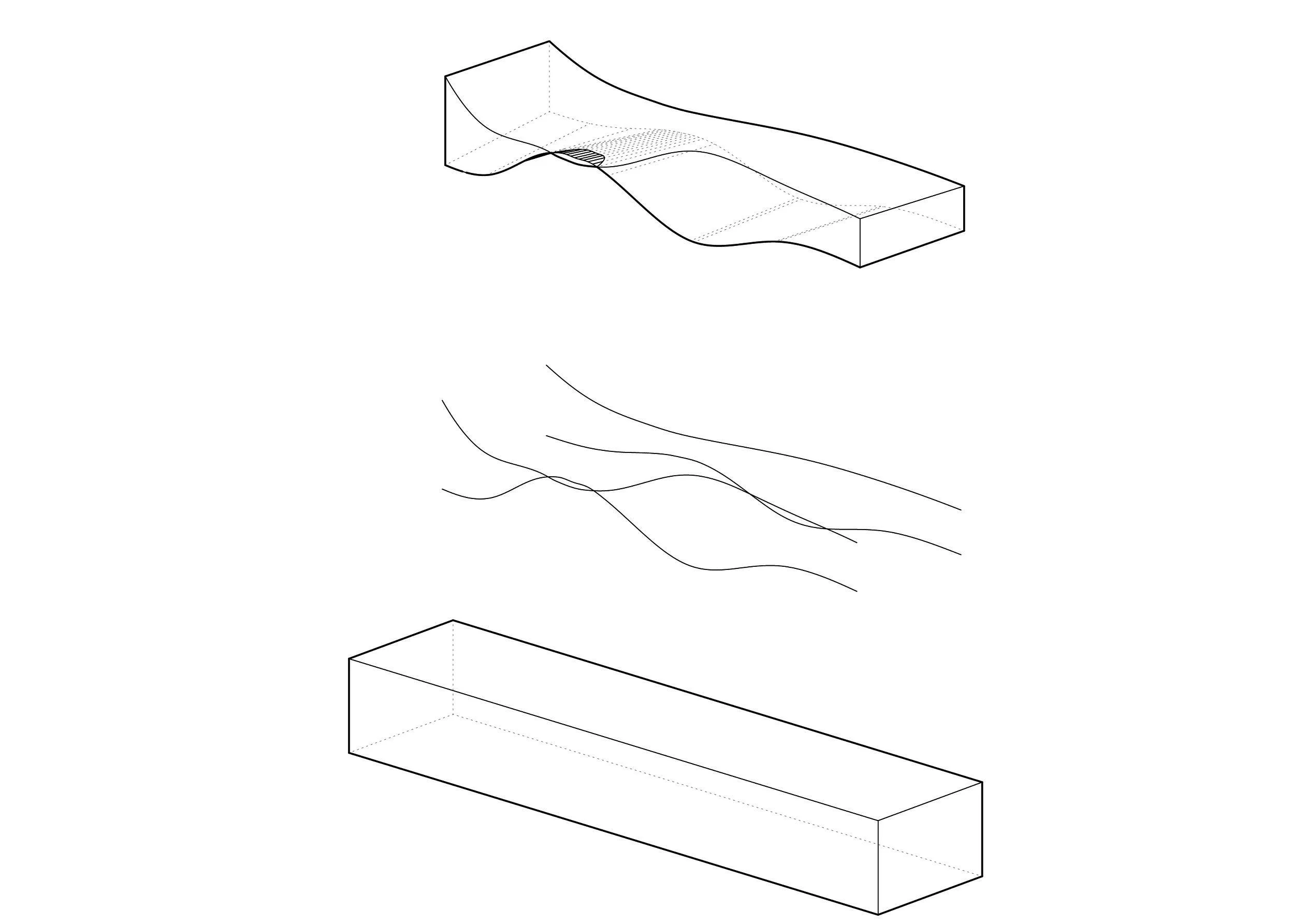
Geometries were translated into lines and points in Grasshopper
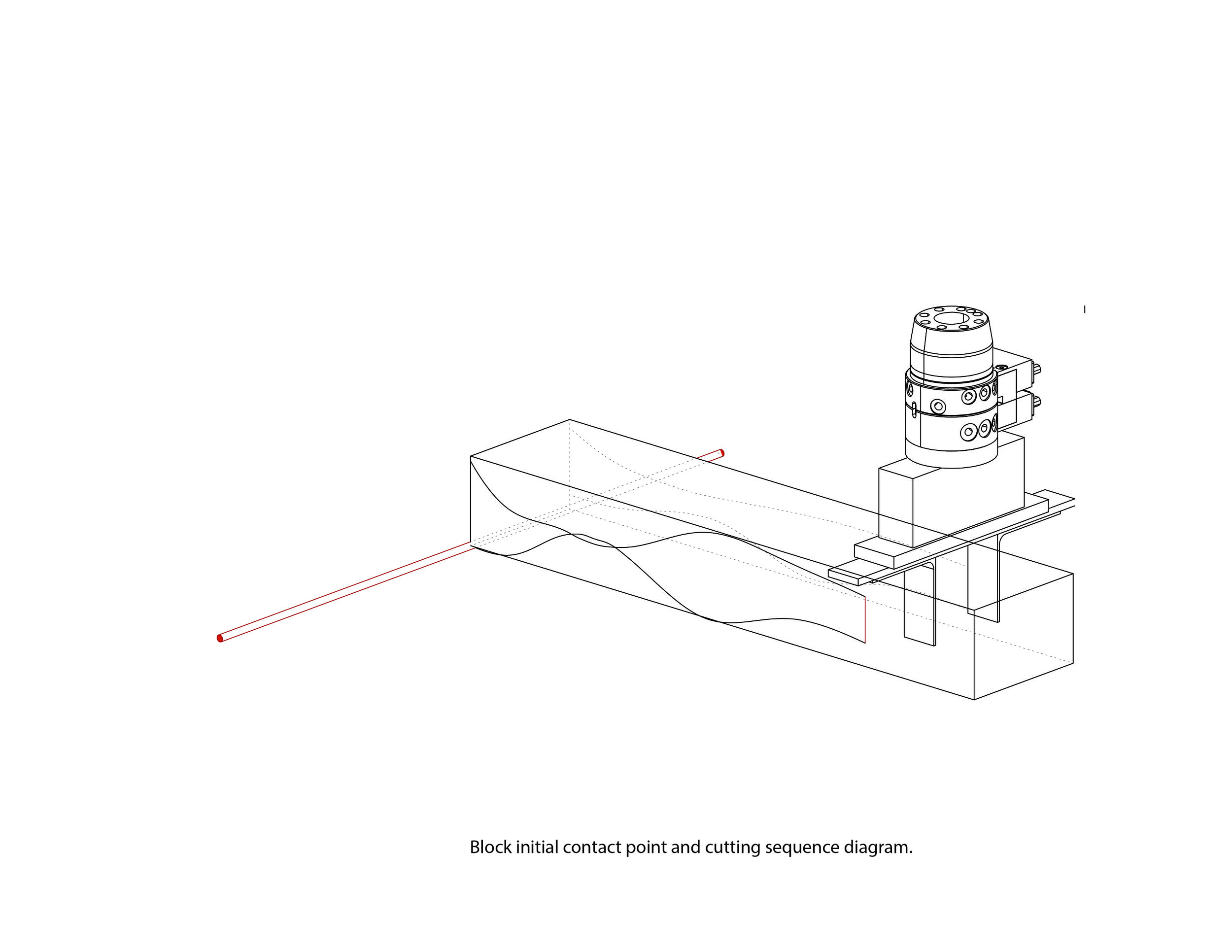
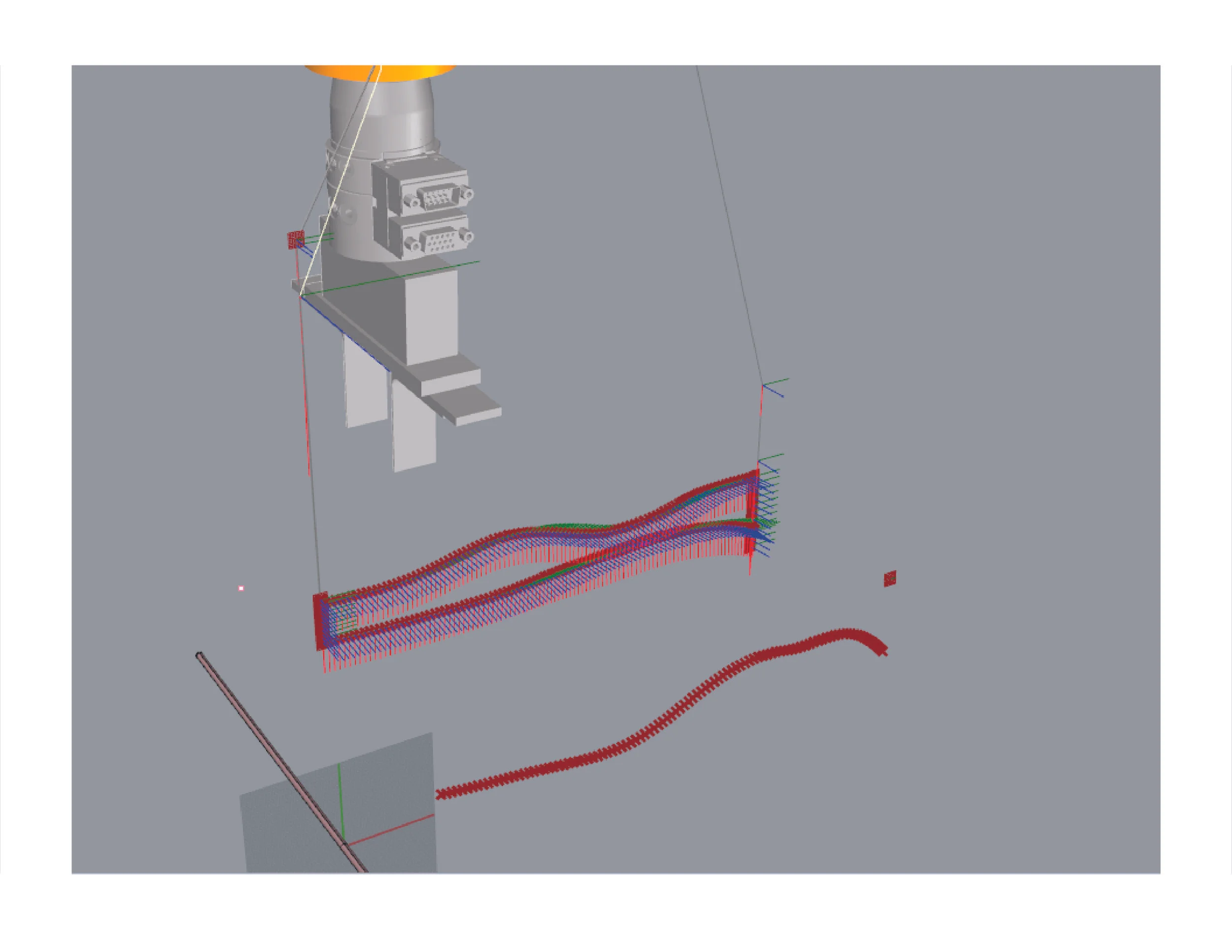
Spatial points became target positions for the robotic movement trajectory, so the robotic arm could cut the target geometry out of our styrofoam block.
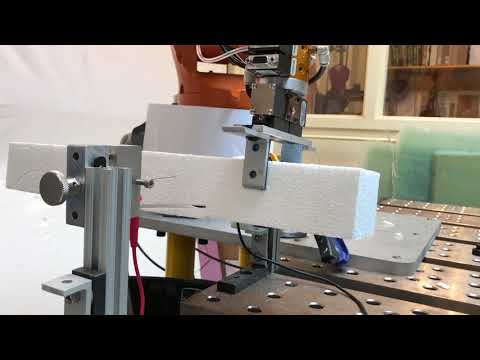
We built a Genetic Algorithm optimization script to make the semi-circular notch as accurate as possible, then fed the generated planes into our Grasshopper script which controlled the robotic cutting path.
Many diverse shapes were cut during our experimentation process.
Because the fabrication method is non-destructive, unlike CNC milling, the negatives of the molds could also be used for casting of plaster or concrete.

Styrofoam pieces were packed in sand and used as molds for lost styrofoam aluminum casting
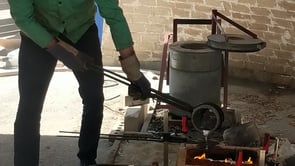
Lost Foam Aluminum Casting

The casting process proved imperfect, but globally accurate in capturing the original styrofoam shape. Further work will be required to refine the minor defects in the aluminum by hand.

The aluminum forms were smaller than the styrofoam, and not perfectly matching the original form
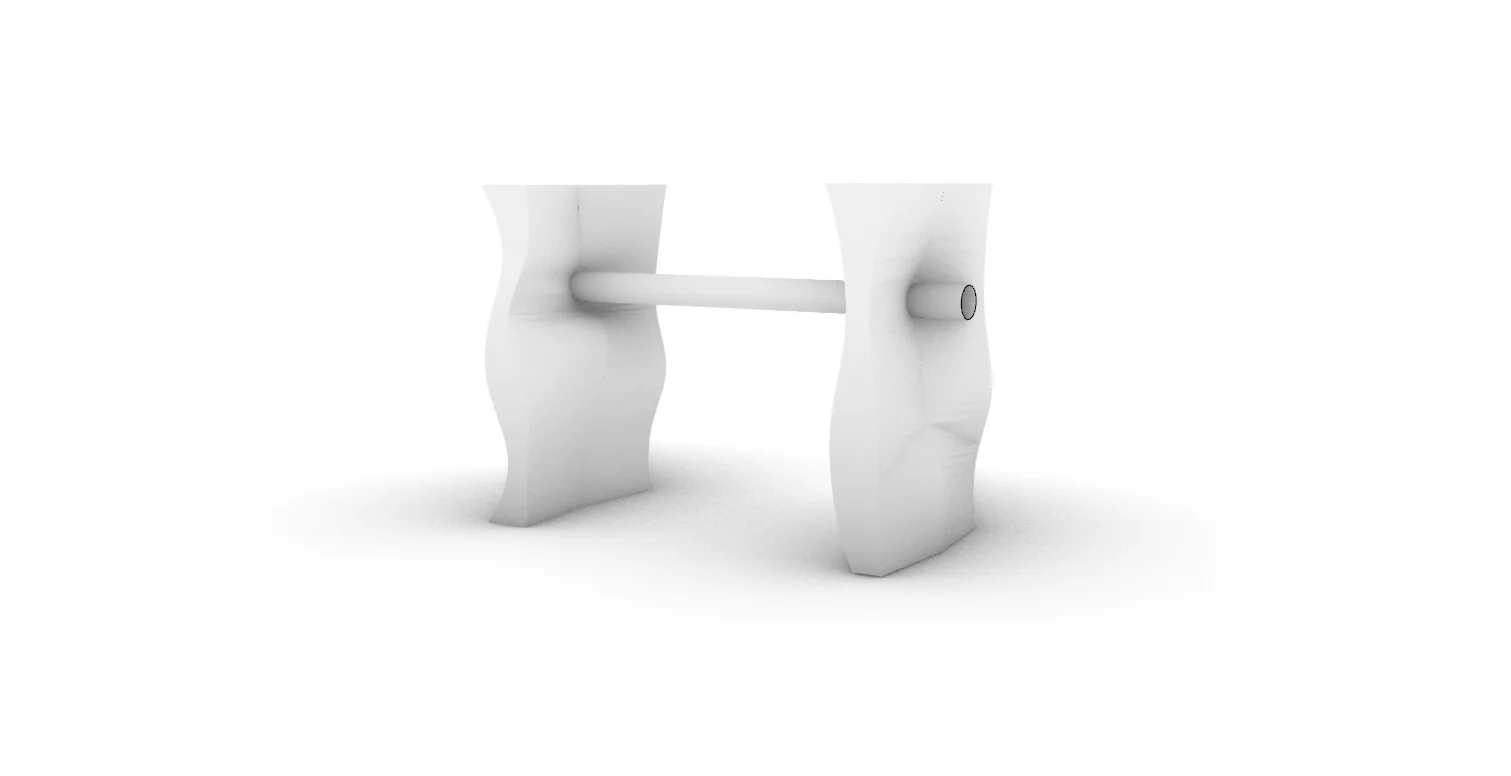


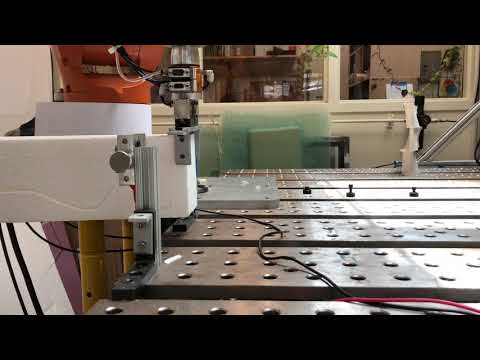
The robotic cutting code we developed is quite flexible, and many ruled surface forms can be used to fabricate diverse forms


This facade form was casted in plaster from the negatives of the robotic cuts. The possibilities of robotic fabrication in the built environment are only beginning to be realized, and this course was an excellent exercise in exploring the potential of robotic fabrication and construction.
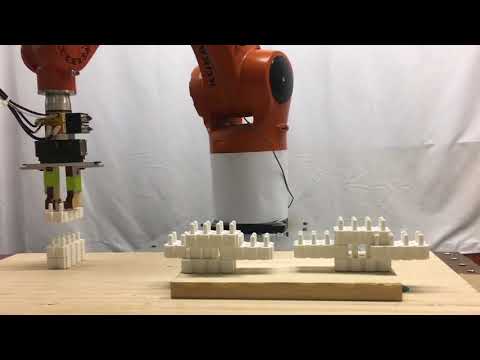
Legoxel Video
For another class project, we 3D printed modular stacking components that could cantilever over long spans, and were easily assembled and dissassembled by our laser-cut robotic end-effector.
(I apologize for the rough editing!)