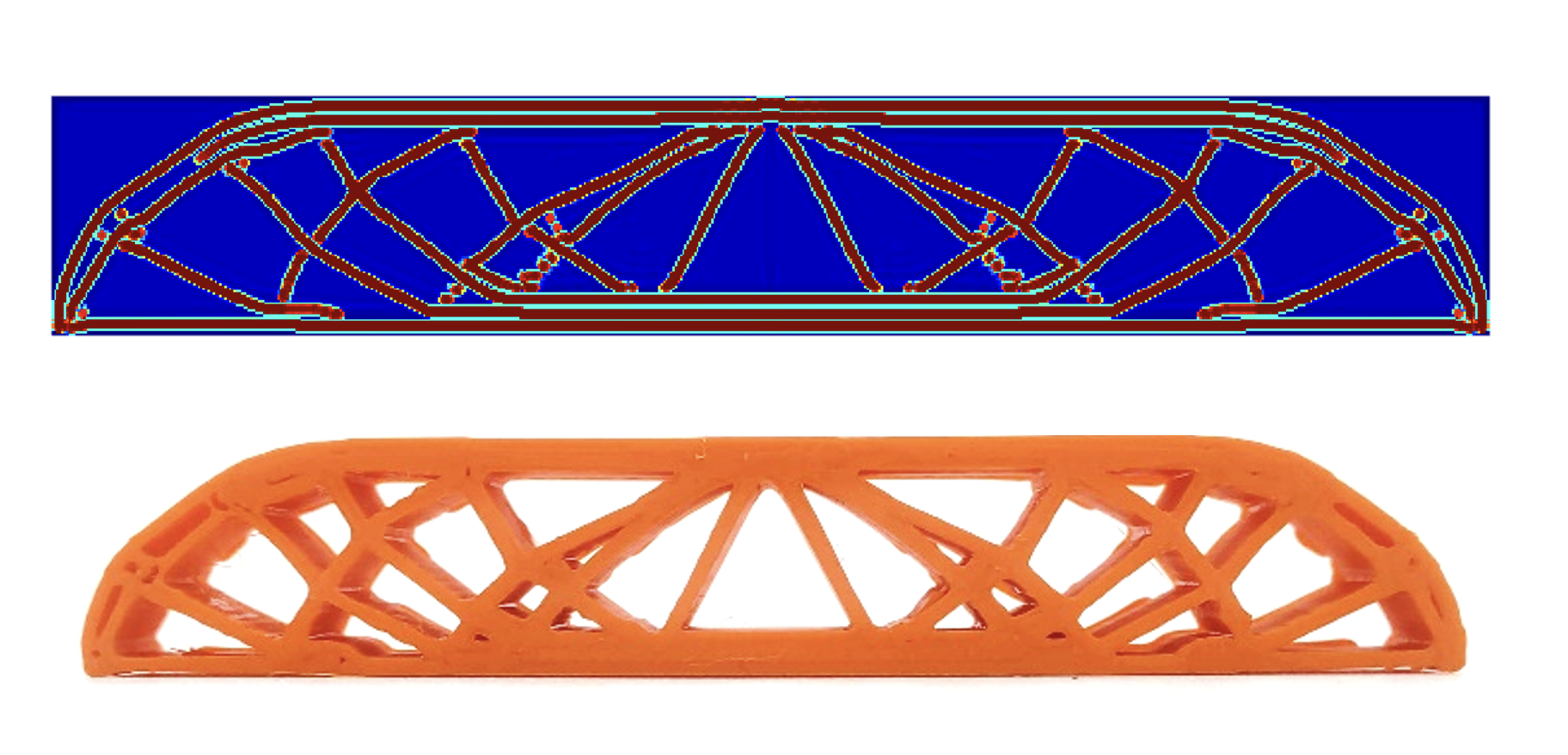
3D Printing Optimization
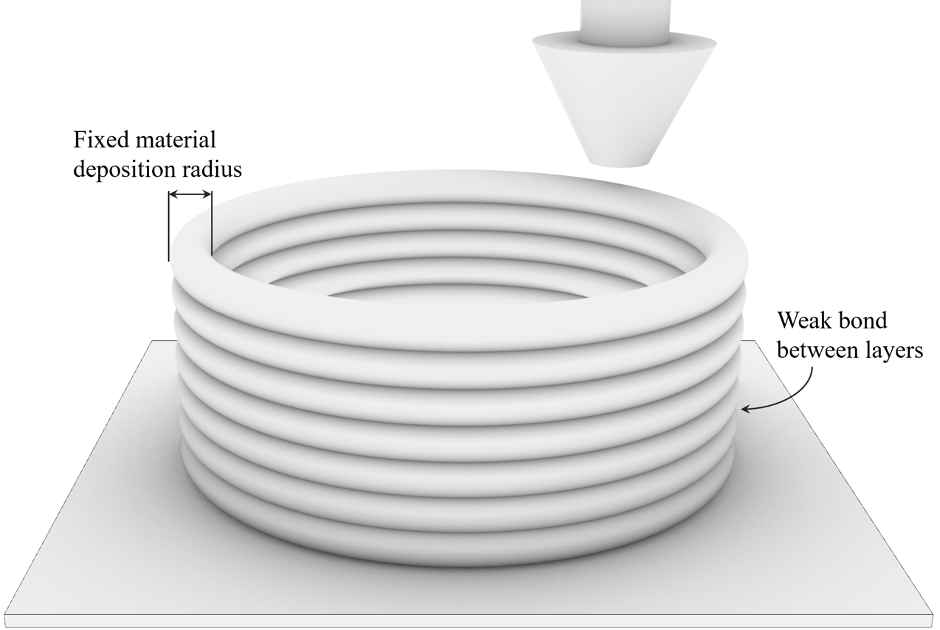
Click on any image for the full paper discussing this research.
In extrusion-based 3D printing methods, material is placed by a nozzle with a fixed deposition radius. The bond between printed layers tends to be weaker than the strength of the material itself. These qualities create constraints on the types of structures that be built using 3D printing, and affect their behavior when forces are applied.

Typical topology optimization algorithms do not consider these constraints. In the above example of an optimized 3-point bending beam, the exact thicknesses of members cannot be captured by discrete passes of a given nozzle size, and the bond weakness between deposition layers is not considered.

My research involved developing a topology optimization algorithm that could generate designs with discrete thicknesses, like the example shown above. It could also apply lower stiffness on the edges of structural members to account for the weak inter-layer bonding in 3D printing.
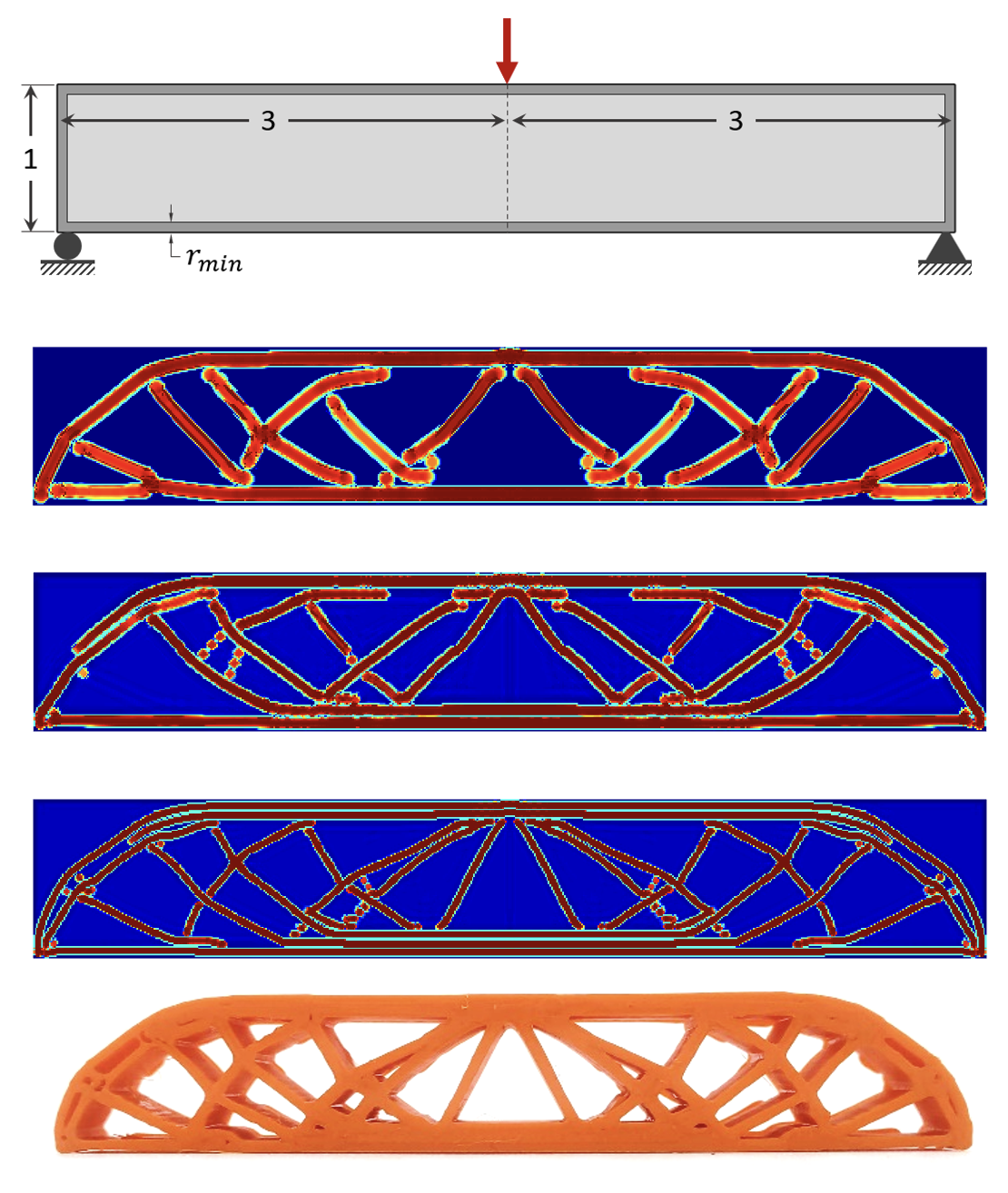
The user can choose the nozzle size when generating results. The algorithm was used to design and fabricate a low-weight 3D printed PLA beam, but the framework could be used for much much smaller systems such as 3D printed steel, or large structures like 3D printed concrete.